Plantrose Product Applications
Demand for sustainable, decarbonized materials in today’s construction and manufactured products is real and growing. From government regulation to consumer demand, the pressure on industry to build decarbonization into their supply chain is strong. Renmatix can meet this demand with powerful materials products, via the Plantrose process technology, to provide solutions for many industries and applications.
Sustainable Aviation Fuel
Aviation Fuel’s Decarbonization Goals & the Shortfall
The U.S. SAF Grand Challenge is trying to fill the gap between supply and demand of ~3 billion gallons by 2030 and ~34 billion gallons by 2050. This is a massive gap between product targets and the projected supply based on today’s pathways to sustainable aviation fuel and the feedstocks currently being used to get there.
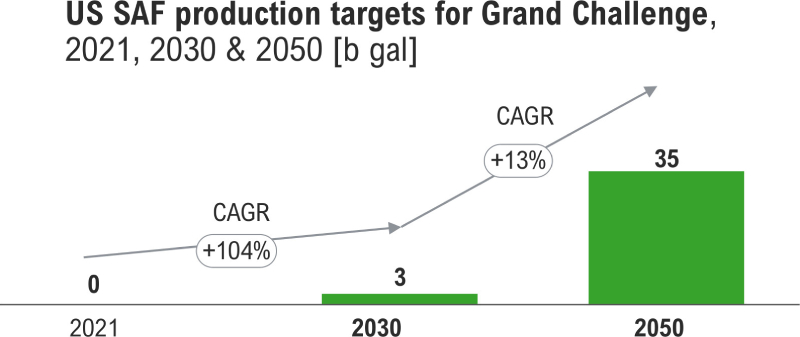
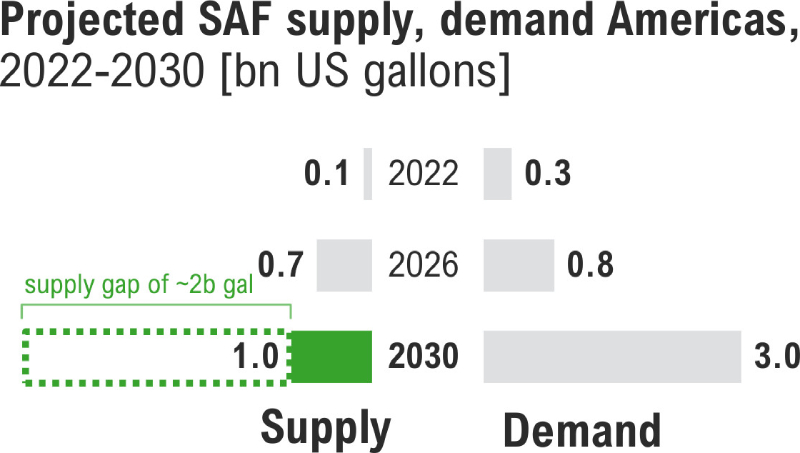
Renmatix Solution
Woody biomass (forestry residues and wood-processing waste) is the largest available feedstock category for making SAF in the U.S. Renmatix is the only proven technology to efficiently and cost effectively process woody biomass to enable SAF pathways to have a significant impact on the SAF gap for both 2030 and 2050.
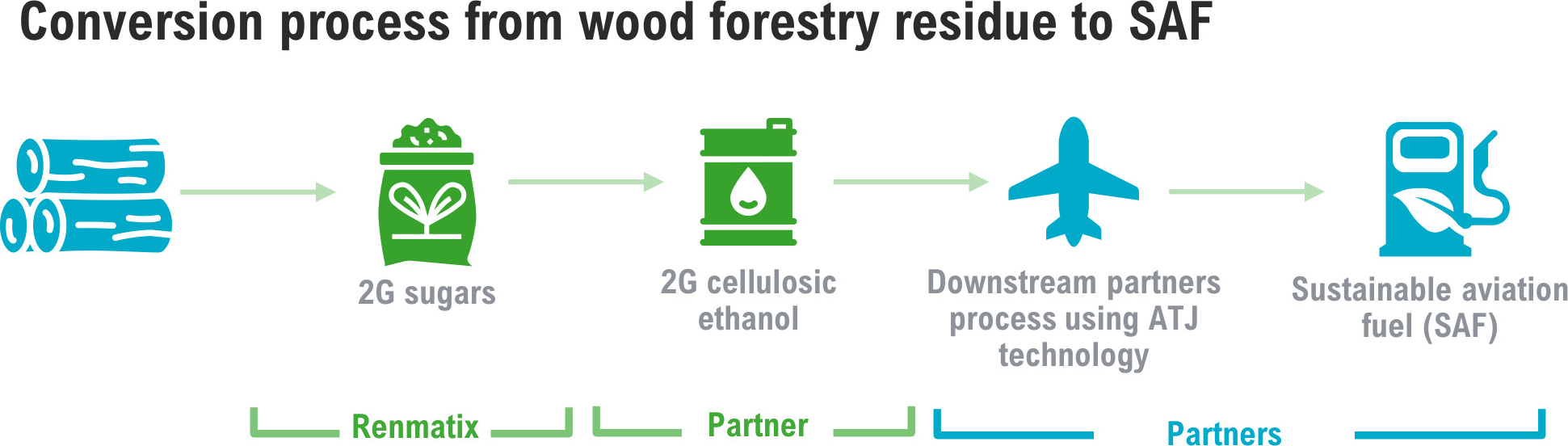
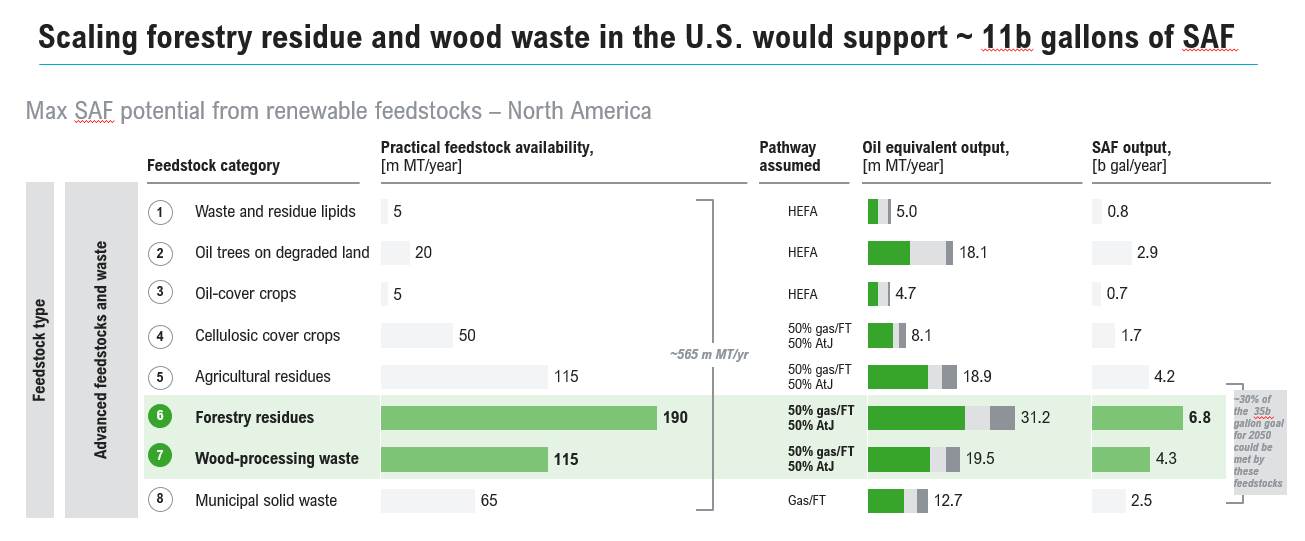
Natural Lignin Polyols to Decarbonize Materials
Decarbonization is real now and market sectors are seeking natural materials solutions with lower CO2 emission profiles. Lignins from the pulp and paper industry are growing in value and use, but continue to have significant issues of both odor and functionality. Omno® lignin and polyol products have no sulfur or other bad odors, are highly pure and highly functional. Its unique composition, size, and functionality are finding favor among lignin and polyol users. Below are some of the applications we are working on with third parties:
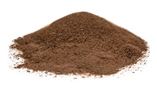
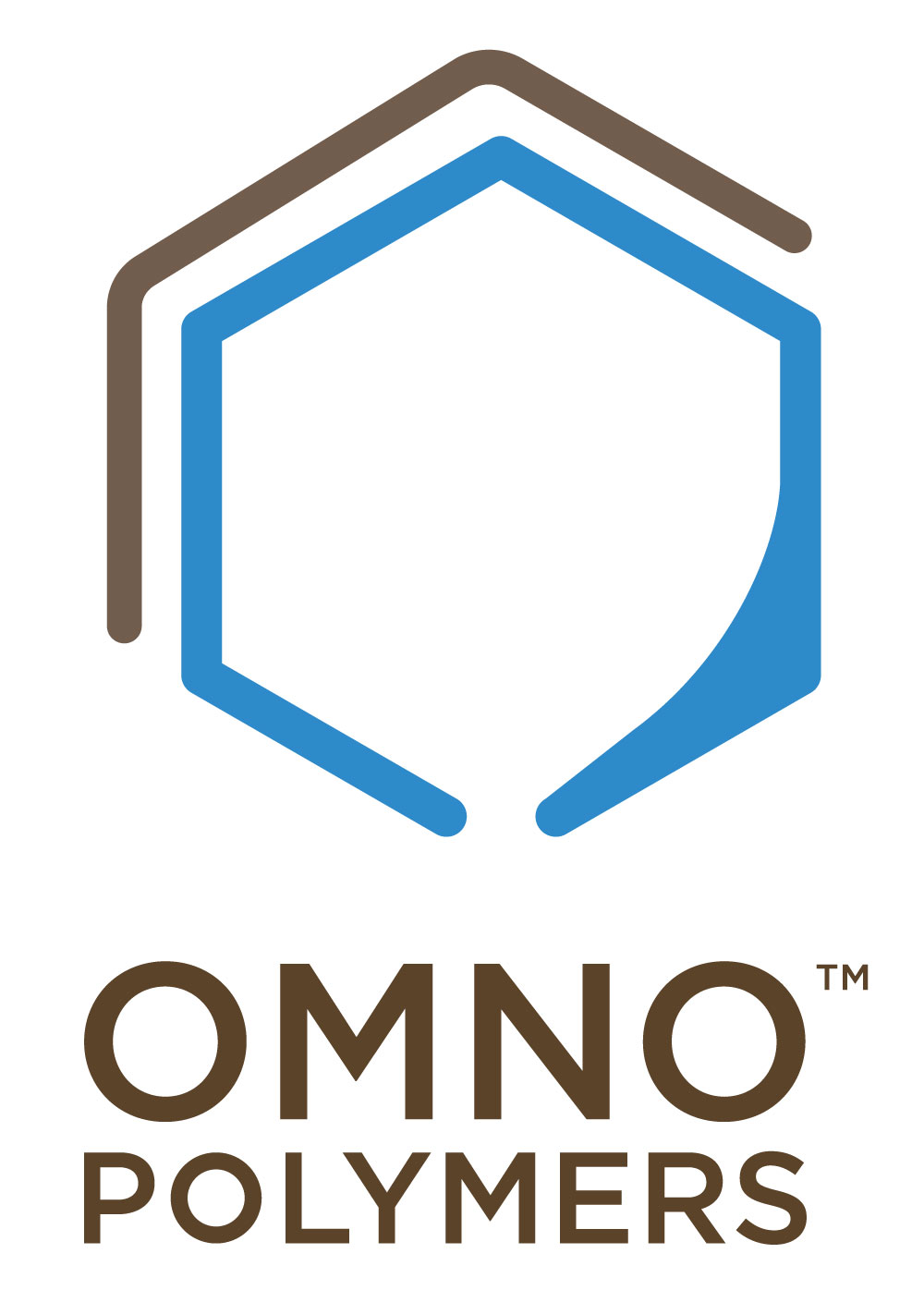
KEY DIFFERENTIATORS
- No odor due to so sulphur content (industrial lignins have high sulphur content)
- Not petroleum derived, unlike phenol or phenolic resins
- Less price volatility in feedstocks
- Tunable carbohydrate ratio
- Higher molecular weight
DISTINCTIVE ATTRIBUTES
- Hydrophobic like waxes
- UV & Thermally stable
- Resistant to microbial activity
- High softening point, amorphous resin
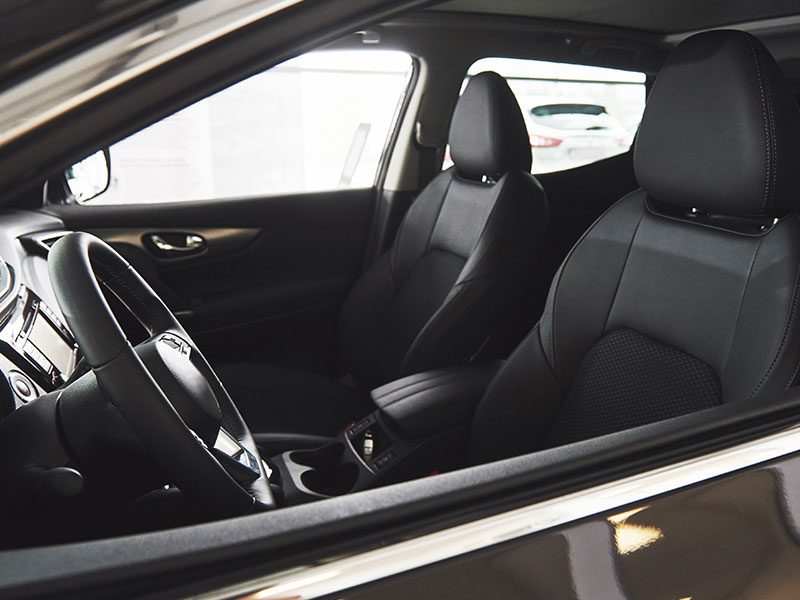
Polyurethane Foams
Manufacturers and their customers are looking for reduced CO2 emissions, while also looking for improved functionality in the foams. Development success for Omno in foams has been encouraging. Use of these foams could impact both market size and timeline, particularly automobile OEM use.
Adhesives
Manufacturers and their customers are demanding low or no formaldehyde emission in engineered wood products. Replacing the phenol formaldehyde resin with Omno lignin and polyol products not only meets the lower emissions goal, but lowers the carbon footprint while increasing the performance of the adhesive.
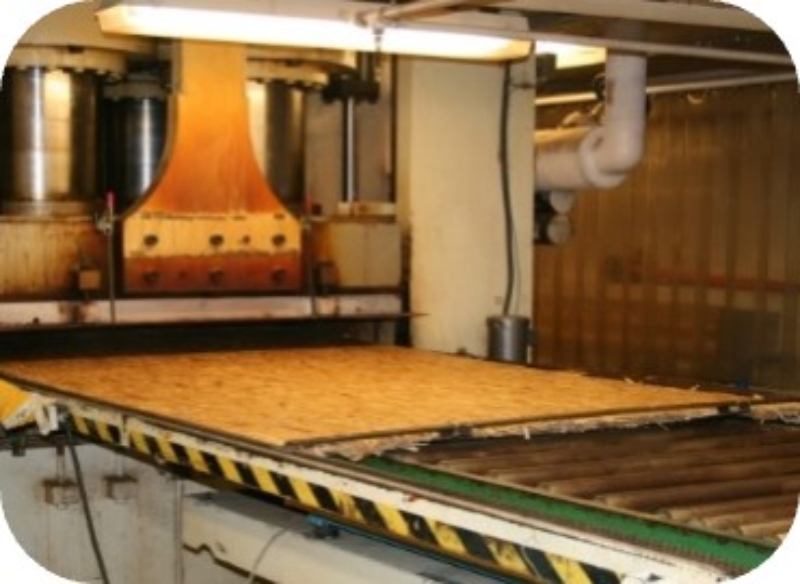
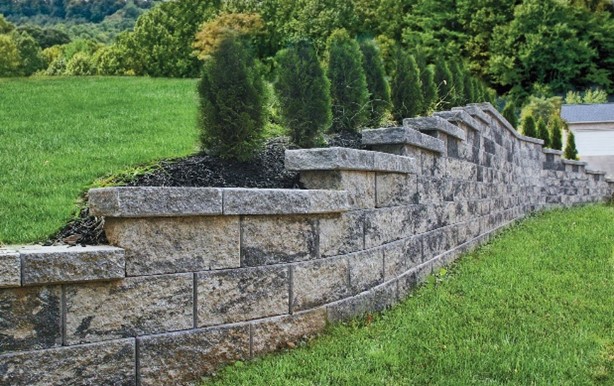
Cementitious Materials
Construction and landscape product manufacturers are looking to reduce the carbon intensity of concrete building blocks, that meet new building standards (e.g., California) and consumer demand. In addition to lowering the carbon intensity of the content and process of manufacturing the cementitious materials, use of Omno products has shown to reduce the weight of these landscape blocks. This will result in further reducing carbon footprint profile of storing, delivering and constructing with the material.
Batteries
Manufacturers of batteries (including lithium-ion and lead acid) are also looking for replacements for the petro-derived materials currently used for some of the elements of batteries in order to lower the carbon footprint while also securing domestic sources of supply. Omno’s purity and functionality hold great promise to meet this demand.
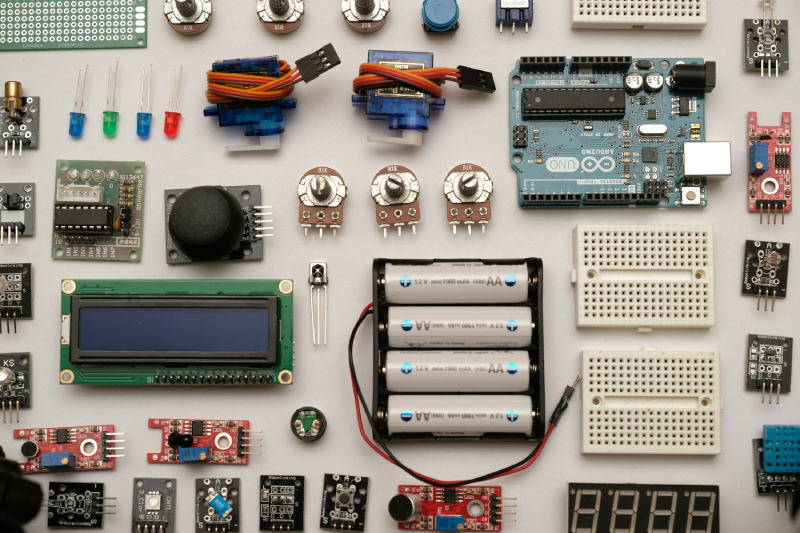
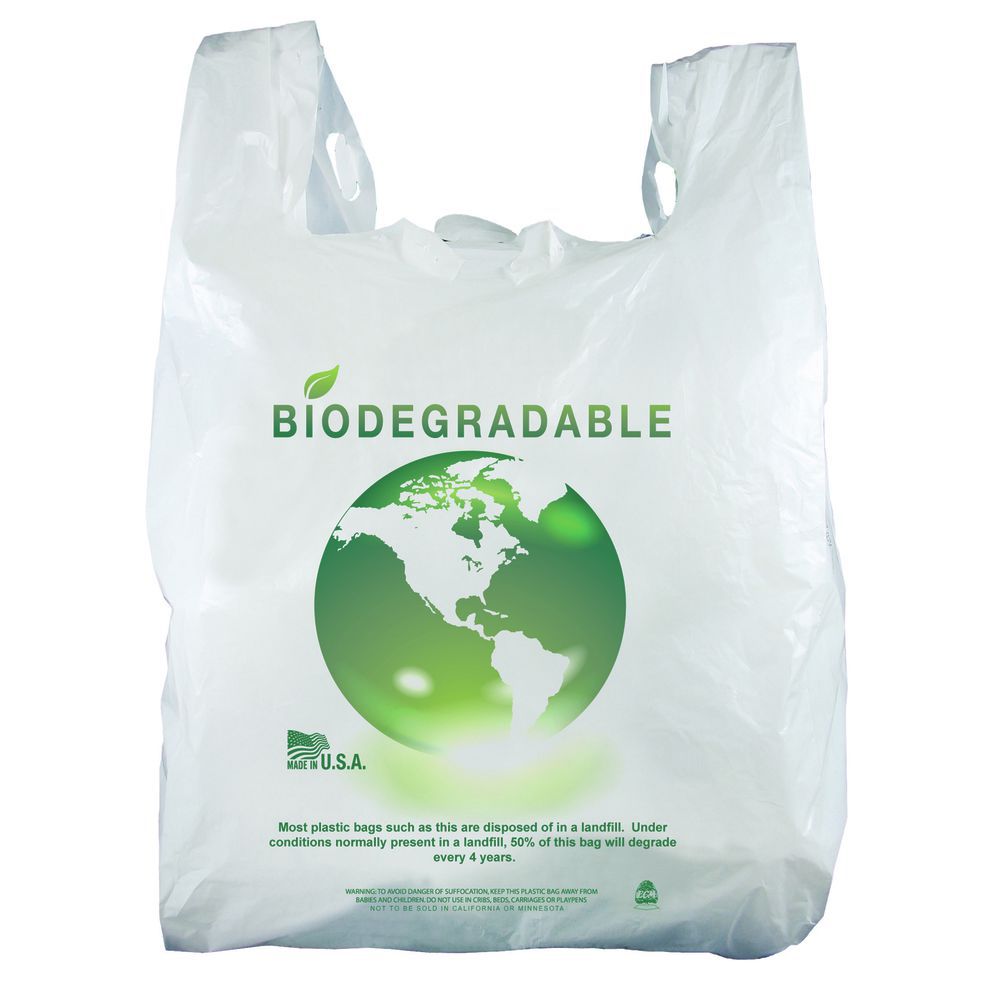
Biodegradable Plastic
Producing a cost-effective, biodegradable plastic that meets consumer needs of particular uses would be a big decarbonization industry win. While lignin seems to be a good option to create these plastics, the odor and functionality issues of lignins from pulp and paper processes have not led to successful products. There is much promise in the use of our clean, odor-free, highly functional lignin for these biodegradable plastics.